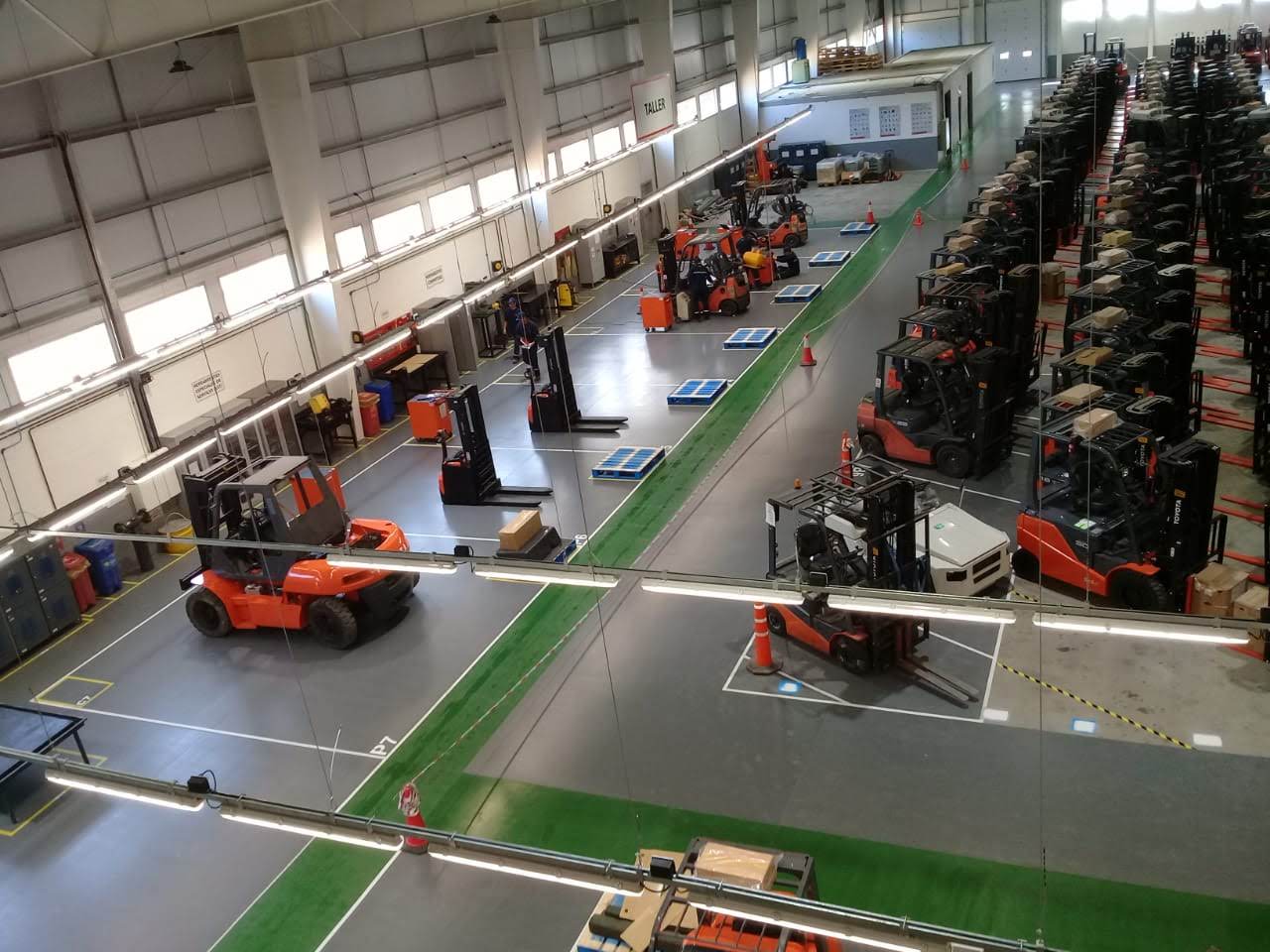
Toyota iba a presentar una nueva planta para su línea autoelevadores. Necesitaban que un piso que superara las auditorías necesarias para poder operar y contaban con un presupuesto reducido. Presentamos la historia de cómo un hormigón desnivelado se convirtió con poco tiempo y a bajo costo, en una planta modelo para abastecer al Mercosur.
La mudanza de la planta para la línea de autoelevadores en Toyota estaba casi lista. La estructura ya se había terminado y las oficinas estaban prontas a instalarse. Una importante obra que estaba destinada a ser punto de distribución para toda Sudamérica, estaba a por comenzar su funcionamiento. La única disyuntiva de la Gerencia residía en nuestra especialidad: los pisos.
La colocación del hormigón había arrojado una superficie muy desnivelada que podía poner en riesgo la seguridad de los trabajadores y las únicas soluciones parecían ser las habituales. Estaba en consideración colocar una carpeta o algún tipo de revestimiento como mármol, porcelanato o mosaico granítico. El único problema era que ese trabajo demandaba más tiempo de obra y la inauguración de la planta iba a contra-reloj, sumado a que el presupuesto destinado ya se estaba acabando. Como plus, los productos de recubrimiento para pisos son habitualmente producto de la mega minería, o contienen contaminantes, idea a la que Toyota se opone tajantemente.
De esta manera, el acertijo parecía conllevar una resolución compleja. ¿Cómo hacer para lograr en poco tiempo, a bajo costo y con resultados de alta calidad sin contaminantes, un piso para seguridad industrial que pasara las auditorías?. La propuesta de OGL fue pulir directamente el hormigón.
Hormigón pulido: Seguridad industrial para los trabajadores
Las tareas comenzaron en el sector de oficinas. El hormigón que se encontraba colocado, rústico y desnivelado, se trabajó con un sentido minimalista. Se agregó vidrio para el embellecimiento de la superficie. Esta modalidad de trabajo se conoce como pulido y vitrificado, que arroja un piso sumamente estético. El mantenimiento es realmente muy sencillo, ya que el cerrado de poros protege al hormigón de manchas y roturas. Así se facilita la limpieza y el brillo constante de la terminación.
Por otro lado, se trabajó en la planta donde se realiza la distribución y mecánica de los autoelevadores. Allí se hizo un trabajo de pulido y preparación de la superficie para pintar. El objetivo de la gerencia de Toyota era que se realizara la demarcación de las calles de circulación peatonal. Este es un requerimiento de las normas de seguridad industrial. De esta manera, la tarea se realizó con dos colores: el verde para circulación peatonal y el gris para circulación de autoelevadores. Al penetrar en los poros, la pintura epoxi logra una gran duración y resistencia al tránsito, sin levantarse.
El resultado fue una superficie sumamente estética, resistente y lista para ser sostén de la planta de autoelevadores más importante de Sudamérica.